More often than not I make my own hose clamps. Mostly because I found a tool a few years ago that just does so much of a better job than the screw gear hose clamps from the hardware store. I was given a ClampTite wire tool and a roll of stainless safety wire as a gift and had no idea what it was. It lingered in a junk drawer, still in the original packaging for a couple of years.
Fast Forward a bit and I needed to connect some water pump hose RIGHT THEN, didn’t have a clamp, and remembered the weird thing in the drawer. This was before YouTube, so I had to read the paper instructions. The little thing worked like a charm! I found uses for it all over the place: poly hose, garden hose, reinforcing my file handles, fuel line on my then truck, a camp stove, capturing hooks on bungee cords, etc. I kept it in the truck because it seemed that I used it like once month. A couple of years ago, I dropped it into the depths of Lake Union in Seattle while doing something crafty with it. I missed that tool very much.
A few months later, I was at the Port Townsend Wooden Boat Festival and there was a dealer there (AKcooltools.com) selling the stainless marine version (my original was aluminum). I told them how much I loved their tool and bought another one from them at the retail show price and I have used the bejesus out of it.
Just for clarification, I am not getting any sort of deal or kickback from AKcooltools or ClampTite or anyone else for this or future planned purchases. I have no financial incentive for make a video about this product. I am just telling folks about something I found that was useful, a quality tool that saves me time, and a seller that was really nice to me and answered all my questions thoroughly.
I am not the only one who has found the ClampTite to be awesome, there are folks on YouTube who use this tool/system on cars, boats, on tool handles, in roadside emergency kits, experimental light aircraft, hotrods, for crafts, fishing, hunting, off-roading, on the farm, etc… for both temporary and permanent fixes. Take a look at the links below the video link and you will see other converts.
I am picking up another one of the aluminum versions for the Jeep and I would also like the heavy duty 10” model that handles 1/8” wire for a couple of large projects that I have planned for winter – saving my pennies.
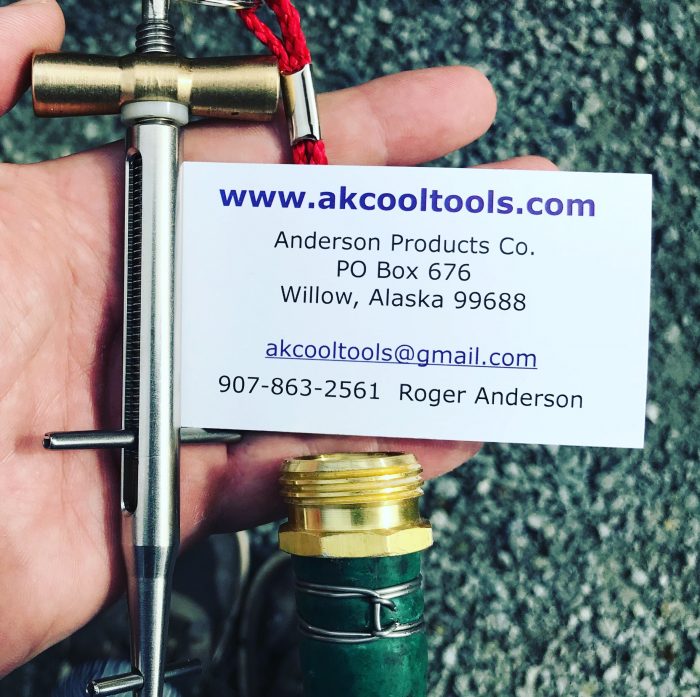